第4次産業革命(Industry 4.0)の到来により、製造業界では激しい技術競争が巻き起こり、私たちの働き方は大きく変化しました。製造の本質は、リソースの最適化、利益の最大化、そして企業価値の向上にあります。
そのため、多くの製造工場では、デジタルトランスフォーメーション(DX)を積極的に進め、プロセスの自動化を図っています。これにより、人間は手作業から解放され、より創造的で革新的な業務に集中できるようになります。
その実現を支えるのが、Manufacturing Execution System(MES:製造実行システム)です。では、MESとは何か?なぜ製造業の革新にとって不可欠なのか?詳しく見ていきましょう。
MESとは?
MES(Manufacturing Execution System)は、工業分野において広く使用されている一般的な用語です。「製造実行システム」として知られるMESは、生産の運用と実行を管理するためのシステムです。その名の通り、MESは、企業が生産活動を実施、監視、最適化するための統合ソリューションです。
MESシステムは、工場内の複雑なデータストリームを接続・追跡することで、生産、保守、品質管理、サプライチェーン管理などの重要な業務に管理者が集中できるようにします。
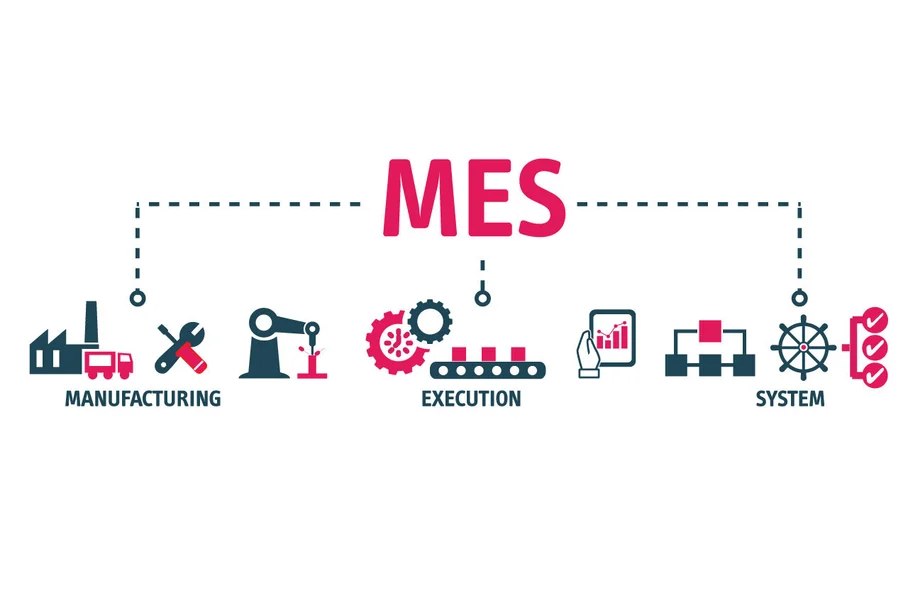
最新のアルゴリズムを搭載したMESの主な目的は、生産活動の効率的な実行を確保し、労働生産性を向上させることです。MESシステムはセンサーと連携し、生産プロセス、パフォーマンス、トレーサビリティ、原材料管理、進行中の作業、およびその他の工場の活動に関するデータを収集します。機械システムがこのデータを処理・分析し、視覚的なレポートを通じてユーザーに送信します。この基盤により、工場管理者は現在の生産状況を把握し、より適切な運用・最適化の意思決定を行うことができます。
スマートファクトリーの中でMESはどの位置にあるのか?
スマートファクトリーは、現在の製造業にとって有望な新たな方向性と見なされています。高度なカスタマイズ性を備えた先進技術を適用することで、プロセスの自動化がよりシンプルになり、新たなレベルへと引き上げられます。
インテリジェントファクトリーの文脈において、MESは生産実行フェーズ(エグゼキューションレベル)の中核となります。MESは生産プロセスと企業の運営システムを結びつけ、稼働中の機械からリアルタイムで収集されたデータを活用します。MESは生産プロセスを最適化し、管理のための重要な情報を提供し、迅速な意思決定を可能にする役割を担っています。
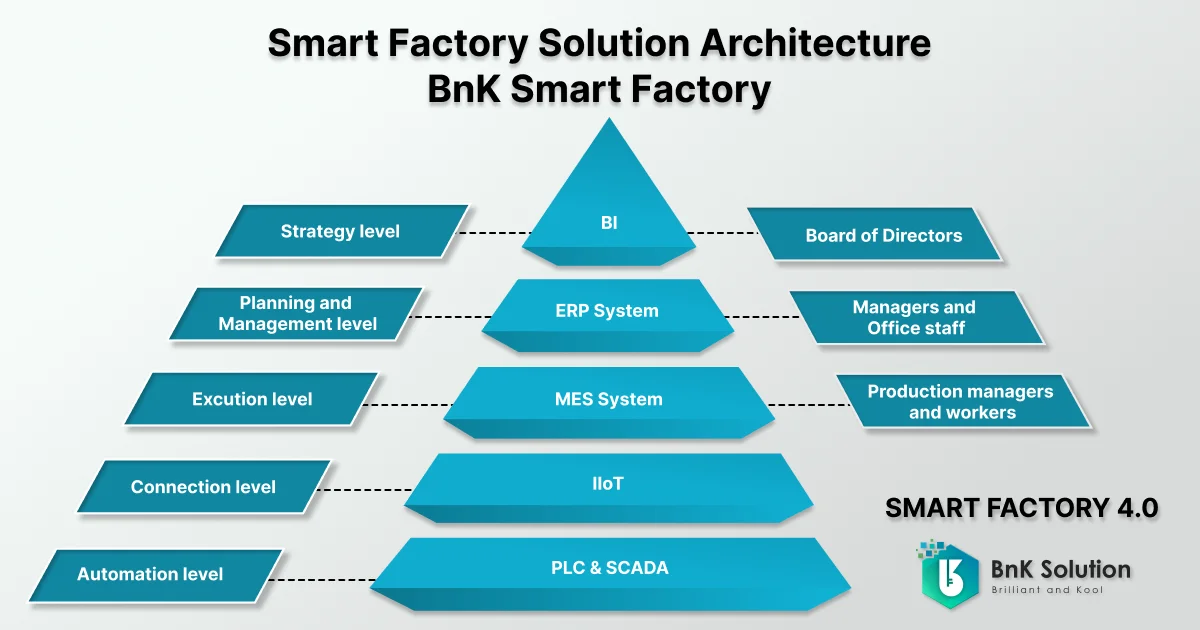
MESシステムは、このレイヤーで決定された内容を直接、生産管理チーム、品質管理、機械オペレーターに展開します。このアプローチにより、企業は従来の方法のように生産段階の終了を待つのではなく、リアルタイムで生産プロセスを更新できるようになります。データ収集、製品検査、品質管理、リソースの最適化といった活動は、MESシステムのリアルタイム監視と運用によって促進され、企業がより効率的な生産プロセスを創造・管理できるようになります。
MESソフトウェアの主な機能
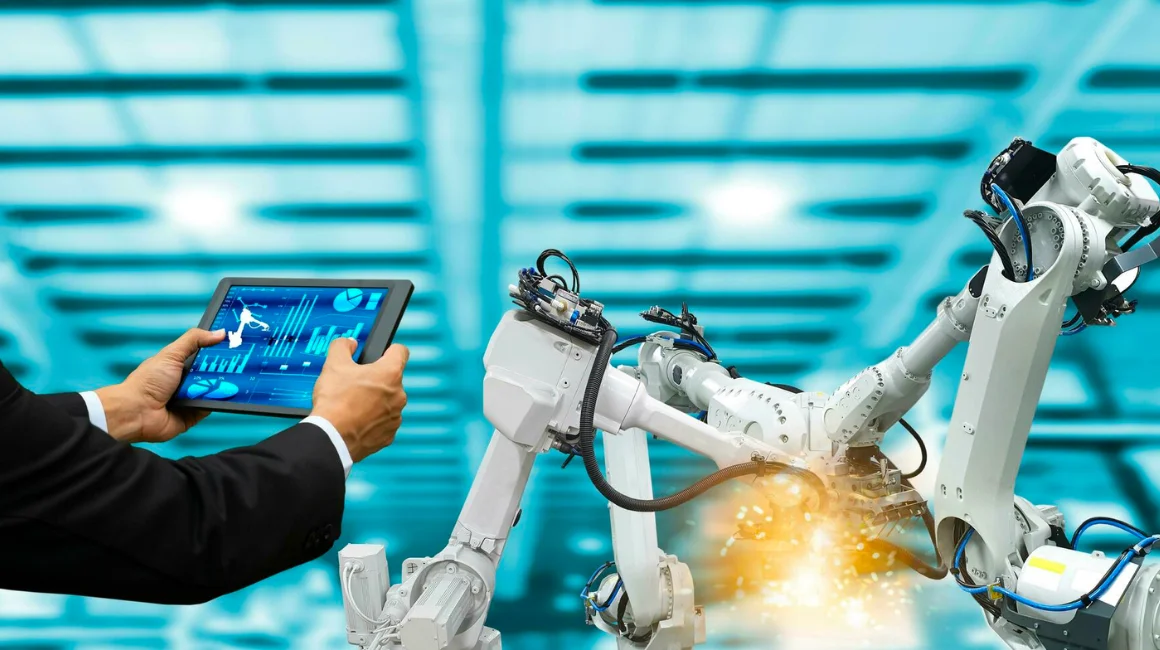
生産スケジュールの設定
MESソフトウェアは、製造業務と運営システムをつなぐ橋渡しとして機能し、ERPシステムから受信した計画に基づいて(ほとんどまたは全く人間の介入なしに)生産スケジュールを自動で設定します。このERPシステムは、企業のリソース計画を管理する役割を担います。
リアルタイム生産管理
MESシステムの強みを定義する主要な機能の一つがリアルタイム生産管理です。
センサーを搭載したIoTやSCADAデバイスにより、機械の稼働時間、停止時間、生産量、耐久性、環境センシングなどのデータを継続的に収集し、中央データ管理ハブへ送信します。ユーザーは、コンピューター、モバイルデバイス、またはダッシュボードを通じてMESシステムに直接アクセスし、工場に物理的にいなくてもワンクリックで情報を監視し、即時の意思決定を行うことができます。
完成品の品質管理(QA)
MESの品質管理機能は、管理者が品質基準を定義し、検査手順を確立し、試験結果を記録し、最終製品が品質基準を満たすことを保証するためのツールとプロセスのセットです。この機能には以下のような活動が含まれます。
品質基準管理
試験サンプル管理
検査管理
データ分析管理
是正措置管理
特に検査は、原材料の受け入れから完成品の出荷や納品に至るまで、基準に応じてさまざまな段階で実施される重要な作業です。MESシステムは、品質情報を単一のデータベースに保存し、レポートの生成、品質情報の検索、アクションの実行を効率的に行えるようにします。
設備管理とOEE
OEE(Overall Equipment Effectiveness:設備総合効率)は、企業の製造業務の効率を評価し、生産性向上のためのアクションをサポートする重要な指標です。OEEの数値は、機械、製造ライン、または設備の適正な稼働時間を示します。OEEが高い企業ほど、設備を効率的に活用し、生産量を増やし、不良品を削減できます。
MESシステムは、工場の製造設備の全体的なパフォーマンスを監視する機能を提供します。設備の稼働準備状況、性能、耐久性などの情報を収集・処理し、中央システムに論理的に表示します。管理者は、ダッシュボードや携帯デバイスを通じて、機械の状態や製造現場のプロセスを把握し、適切なアクションを取ることができます。
MESシステムを活用することで、リソースの使用が最適化され、機械の稼働を継続的に最適化することでダウンタイムを最小限に抑えることが可能になります。これにより、生産効率が向上し、アウトプットが増加し、資源の無駄を削減できます。
材料管理
材料管理は、生産プロセスのスムーズな進行と最終製品の品質を保証するための重要な段階です。
工場に統合されたMESソフトウェアは、材料の供給と使用を管理し、生産時の材料消費を適正化します。さらに、このツールには以下の機能が含まれています。
原材料の在庫レベルの追跡
新規発注の管理
材料の適切な使用の保証
これにより、企業は材料不足によるダウンタイムを防止し、業務効率への影響を最小限に抑えることができます。また、生産廃棄物の発生要因を特定し、無駄の削減にも貢献します。
バーコード管理
MESのバーコード管理機能は、生産中の製品を追跡・管理するための効率的な手段を提供します。製造プロセス中に製品や材料にバーコードを追加することで、各製品の位置情報、詳細情報、在庫数量を正確に把握できます。
原産地トレーサビリティ管理
MESシステムのもう一つの機能は、各完成品や生産バッチごとにバーコード、RFID、QRコードを自動生成する能力です。これらのコードには、メーカー、供給業者、販売業者などの情報が含まれており、誰でも迅速に製品の出所を追跡できるようになります。
これにより、企業は生産・流通過程において安全性、品質、規制遵守を保証しながら、顧客の信頼を築くことができます。
レポート抽出
MESシステムは、生産プロセス、設備のパフォーマンス、製品品質、その他の特定の要素に関するレポートを生成・提供することができます。これにより、管理チームや生産チェーンの他の部門は、リアルタイムデータを含むレポートを確認し、工場内の生産状況を把握し、業務の最適化を進めることができます。
レポートには、統計データやリアルタイム情報が含まれており、業務のパフォーマンスを包括的に分析するための貴重なリソースとなります。
MESシステムの強み
MES(製造実行システム)の強みは、さまざまな要因によって形成され、堅牢で信頼性の高いシステムを構築します。特に、以下の3つの要素が、MESの優れた機能を支える重要なポイントとなります。
マルチソースデータ収集能力
MESは、以下を含む複数の情報源から同時にデータを収集できます。
製造設備のデータ(機械、オートメーションデバイス、制御システム)
生産プロセスのデータ(生産スケジュール、各工程、オーダープロセス、計画)
外部データソース(原材料供給、市場動向、顧客の嗜好)
これらのデータは、自動的に収集されるか、管理者によってアップロードされます。収集された膨大なデータが、MESシステムが次の重要な処理を実行するための基盤となります。
効率的なデータ分析能力
MESシステムは、高度なアルゴリズムとツールを活用し、データを処理・分析し、工場の現状を把握しやすくします。これにより、トレンドの特定、問題の検出、全体的なパフォーマンスの向上が可能となります。
リアルタイム情報提供能力
自動化された製造工場では、機械が組立ラインで稼働し、各コンポーネントのシームレスな連携が業務効率を向上させます。しかし、適切な警告措置が取られないと、リスクが高まります。MESシステムに継続的に更新される機械や生産プロセスのリアルタイム情報により、ユーザーは適時・正確な意思決定を行い、生産性向上とリスク低減を図ることができます。
MESのビジネスメリット
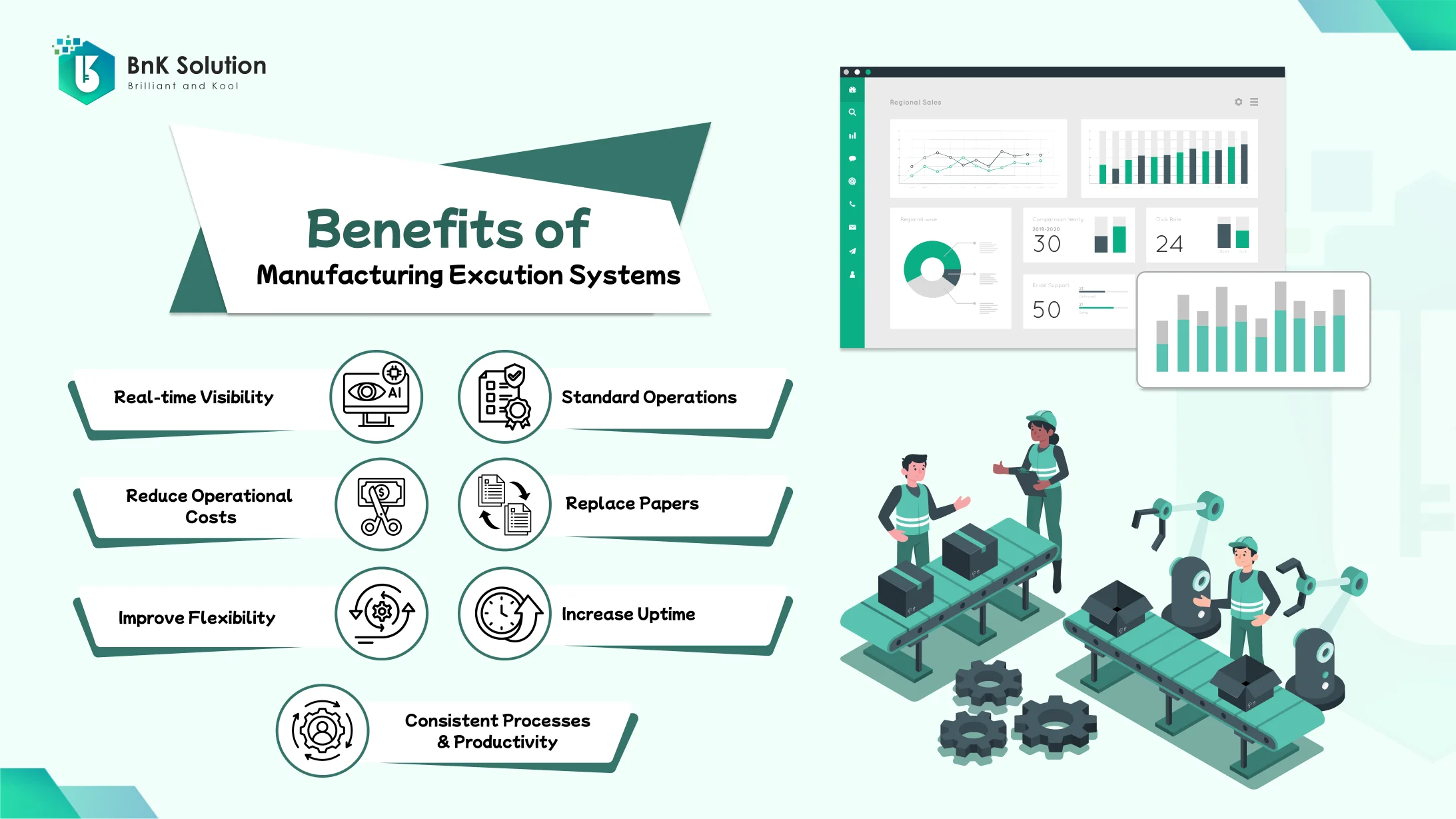
業務効率の向上
受入業務の迅速化、材料準備の最適化、生産材料の待ち時間を短縮。
製品エラーの削減、規制遵守の向上、製造プロセスの改善。
原材料の投入から機械、プロセス、出荷・配送までの生産状況を可視化。
利益の向上
生産プロセスに関する迅速な意思決定をサポート。
コストと企業リソースの削減。
停止によるダウンタイムを最小限に抑える。
生産量、品質、業務効率の確保。
純利益の向上と顧客ロイヤルティの強化。
リスクの軽減
製品品質問題のリスクを低減。
納期遵守の信頼性を向上。
透明性のある生産管理による顧客体験の向上。
よく発生するエラーの予測と予防。
不要なコストや回避可能なリスクを制限。
ERPソフトウェアを導入している企業にMESは必要か?
多くの成長企業ではすでにERPソフトウェアを導入しており、MESを組み込むことで機能の重複が発生するのではないかと懸念されています。しかし、ERPは工場の合理的な計画を構築するために設計されており、MESは機械の運転や製造プロセスなど、より物理的な運用に焦点を当てています。
ERPシステムは、製造プロセスの詳細情報や、個々のコンポーネント・設備の生産能力を含んでいません。そのため、ERP内の計画を具体的な行動に変換するための仲介ツールが必要です。MESが導入される前は、製造管理チームや各機能部門の責任者がこのプロセスを手作業で行っていました。
MESを導入することで、ERPの要求や計画に基づいて具体的な生産プロセスを確立し、最初から一貫した監視を行うことができます。逆に、MESはERPに対して、製造活動、機械の状態、原材料の状況などのリアルタイムで高精度な情報を提供します。この情報を基に、ERPはデータを分析し、次回の生産計画の改善を行います。
MESの機能は財務管理、顧客対応、請求管理などの領域には及びません。MESは工場の製造活動に特化しており、正確な監視とデータ収集を可能にします。企業の製造活動と営業、販売、調達、人事管理、財務・会計業務を統合するには、ERP(企業資源計画システム)が必要です。
さらに詳しく読む >>>
要するに、企業がすでにERPソフトウェアを導入している場合でも、MESをシームレスに統合でき、機能の重複を心配する必要はありません。ERPとMESはそれぞれ異なる目的と機能を持つため、どちらも企業向けの主要なツールとして役立ちます。特にMESの強みを活かすことで、製造プロセスがより論理的かつ効率的に進み、オートメーションの新たなレベルへと向上します。
製造工場にMESを導入する方法
近年、多くの企業がMESシステムの導入に成功し、大幅な成長を遂げています。これは業界全体およびベトナム経済にとってポジティブな兆候です。しかし、製造業における技術適用の競争は激化しており、成長の可能性と顧客満足度を巡る熾烈な競争が続いています。技術の進歩を活用する企業は、チャンスを競争優位性へと変え、市場での地位を確立できます。
企業の特性に適したMESシステムを導入するためには、以下のような重要なステップを踏む必要があります。
目標の明確化
リソースの準備(人材、資金など)
MESプロバイダーの選定
導入計画の策定
システムのインストールとトレーニング
データ分析と効果測定
この中でも、工場の現状を把握し、適切なMES導入パートナーを選ぶことが最も重要なポイントです。
最後に、MES導入に関する課題に圧倒されていると感じたら、製造業向けMESシステムの構築方法を詳しく調べてみましょう。BnK Solutionの知見を活用することで、MESの実行システムについてより深く理解し、自社に最適な方向性を見極める手助けとなるはずです。