Smart factories are a prominent solution for transforming the way production is managed through the application of modern technology platforms. Not only in Vietnam, but many businesses worldwide have also researched and successfully implemented this solution into their production systems.
However, some businesses remain hesitant and concerned, not yet ready to transition to the smart factory model due to the significant changes it brings, essentially requiring a complete overhaul of their current production processes. The reality is that the Smart Factory model brings numerous potential opportunities for the future development of businesses, in a market where demands are constantly unpredictable. If you find yourself in a state of uncertainty and unclear intentions, then this article is for you!
The Outstanding Features of the Smart Factory Model
In recent years, manufacturing enterprises worldwide have been actively participating in digital transformation, improving operational processes, and transitioning to the Smart Factory model. This indicates that the Smart Factory holds vast potential that business owners can hardly ignore. Typically, a Smart Factory includes the following five key features:
Connected
The connectivity feature forms the real power of a Smart Factory. IoT technology provides connectivity, enabling the system to deeply exploit and effectively utilize all data sources within the organization.
In a smart factory, all machinery, equipment, and management systems must be fully interconnected. Every device and machine in the factory are equipped with sensors, allowing production data to be continuously collected and transmitted to the central system. Through MES software (Manufacturing Execution System), users can query information, monitor all processes in the factory, and make important operational decisions based on real-time data.
Connectivity is also the top crucial feature that makes the Smart Factory model superior to traditional manufacturing models.
Optimized
Thanks to the application of artificial intelligence (AI) and advanced automation technology, the operations of the Smart Factory are optimized, allowing machinery and equipment to operate with minimal manual intervention and maximum accuracy.
Moreover, in the modern manufacturing factory model, processes are synchronized, and repetitive mundane tasks are programmed for machines to perform. Humans are gradually being freed from simple tasks to freely apply their minds to researching new technology solutions as well as analyzing and upgrading factory infrastructure.
The management system of the Smart Factory also provides tracking, forecasting, and planning capabilities. As a result, production processes are optimized for energy consumption, time, and operating costs. The smooth coordination between humans and machines through technology connectivity helps smart factories operate more efficiently, improve product quality, and increase productivity. This is why the Smart Factory has become a trend in the transformation of the current production model.
Transparent
In the Smart Factory model, data about machinery, processes, products, and production status are continuously collected in a comprehensive and detailed manner. Real-time visual data is converted and statistically presented in various forms, ready for the next actions of humans or programmed for machines to make automatic decisions.
In addition, data within the Smart Factory system is managed according to levels, providing access capabilities for users based on roles and predefined permissions. The system also has alerts and real-time data extraction notifications to ensure effective security management and operational decision-making.
Proactive
In an automated system, employees and system operators can completely predict and make important, preventive decisions before something negative happens to their production work, rather than waiting for troubles to happen first.
Information about a standard production process can be analyzed and important points can be recorded. These could be information about the raw materials needed to produce a finished product, the operations of machinery, inventory management, and incoming goods management. It could also be the ability to identify anomalies, predict and solve quality issues, or monitor maintenance concerns. All of these data help managers make timely decisions, ensuring that the production and operation processes run smoothly and efficiently, avoiding unnecessary risks.
This is an important feature that a production system with loosely connected components might struggle to achieve.
Agile
The flexibility of the Smart Factory is demonstrated in the factory system’s ability to quickly adapt to changes in production schedules and innovation opportunities with minimal human intervention. Advanced factories can also self-configure machinery, materials, and processes based on the target product type.
In addition, flexibility can increase machine operating time, reduce waste time, and increase factory productivity by minimizing changes due to planning or product changes, while still allowing users to plan flexibly as desired.
The real power of a Smart Factory lies in its ability to evolve and develop continuously throughout the organization’s change process, regardless of the impact from changing market demands, business scale expansion, product and service improvements, or the integration of new technologies and processes. A promising future production management model.
Why are Smart Factories “trending”?
The Smart Factory solution is designed comprehensively, including specialized modules that are seamlessly integrated with each other, ensuring flexibility and suitability for a variety of business types. Below are some important modules in the Smart Factory solution:
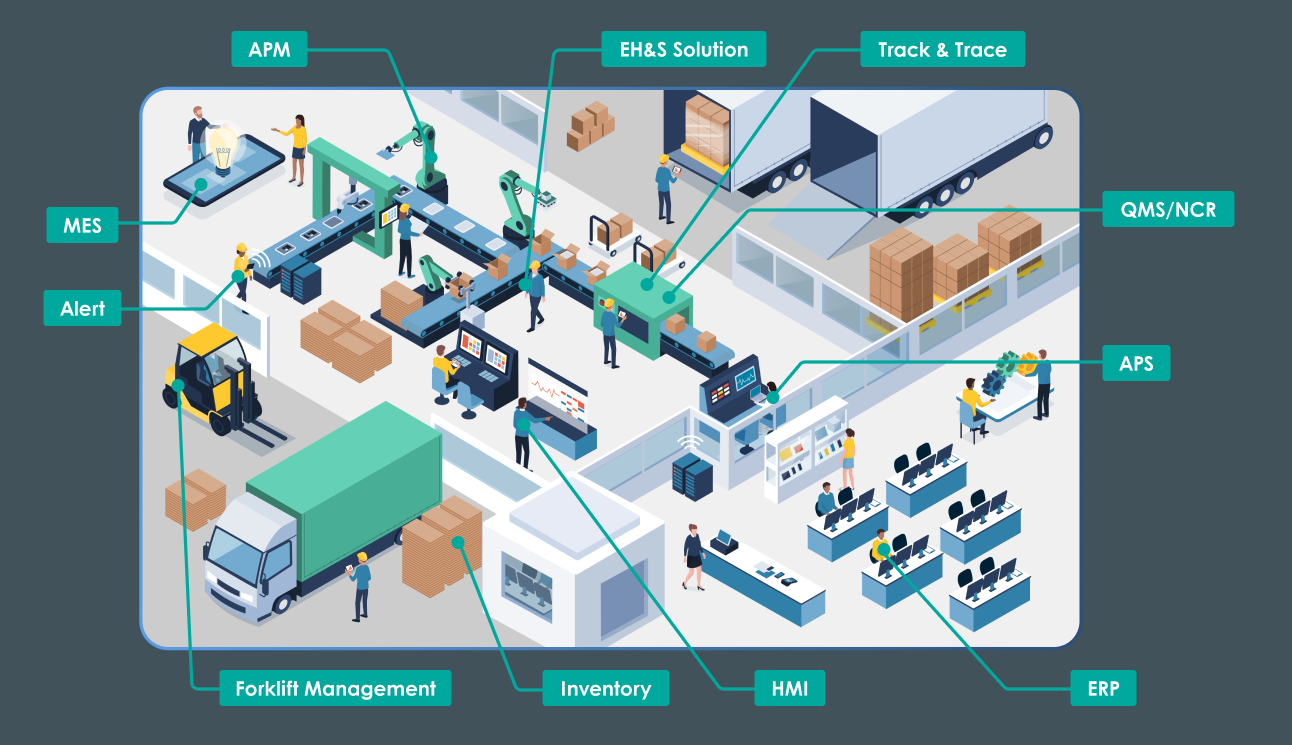
The Smart Factory is a factory model that applies advanced technologies of Industry 4.0 to solve production problems. Each business has different needs and problems, therefore, the benefits that the Smart Factory brings cannot be exactly the same for every organization. A factory is truly smart when all machinery and equipment can maximize process improvements through automation, optimization, and bring practical values to manufacturers. Some outstanding benefits of the Smart Factory are:
Potential for significant productivity growth
The first benefit that most managers are interested in is the growth potential in productivity and output of the production process. Smart factories optimize this by maximizing the productivity of both machines and humans. Thanks to advanced automation technology, humans are freed from simple, repetitive tasks to perform data analysis, create higher customer experiences, and innovate production processes.
In addition, machinery can replace humans to work continuously with high precision and speed, even can work continuously for many days without rest, this helps shorten the production process, ensure the set output level, even far exceed the initial expected output level.
Minimizing Operational Costs in Manufacturing
Production processes in a smart factory are optimized compared to traditional models. Smart machinery systems can operate continuously without manual intervention. Tasks such as inventory checks and data analysis, once reliant on human effort, and prone to human errors, can now be efficiently handled by machines, sensors, and artificial intelligence. This not only saves a considerable amount of labor costs but also ensures accuracy.
Equipment within the factory is now interconnected, and real-time data is continuously collected and transmitted to a central system. This allows managers to make precise operational decisions and even establish automated processes easily. The digitalization of the factory provides a foundation for businesses to eliminate unnecessary processes, ensuring production consistency with lower costs and reduced resource wastage.
Enhancing Product Quality
One of the significant benefits of a Smart Factory is the potential to improve product quality. Equipped with sensors and precisely programmed systems, machinery can closely monitor production processes and detect errors immediately. This minimizes the production of defective products and waste. Machines are programmed to operate accurately and consistently, ensuring uniform product quality.
In a smart factory’s production line, the rate of defective products and the factors causing defects are minimized.
Maintaining and Improving Competitive Advantage
When you can work faster, smarter, and more cost-effectively than your competitors, it translates to delivering more value and attracting more customers. An optimized process enables you to achieve more by producing high-quality products in larger quantities, even with similar or fewer raw materials compared to competitors.
You can better satisfy customers, operate more efficiently, and maintain high product quality, making you more valuable in a competitive market. The competitive edge gained by implementing the Smart Factory model sets you apart while others may struggle to meet production deadlines and avoid incurring extra costs.
Accurate Predictions and Timely Maintenance
A long-term benefit of incorporating machine learning into your processes is the ability to predict and maintain. By collecting and analyzing real-time data, the system can control machine operation parameters, detect anomalies, schedule repairs and maintenance to ensure smooth and continuous production. Understanding machine status through detailed reports and maintenance timelines also helps reduce unexpected repair costs and equipment replacement risks.
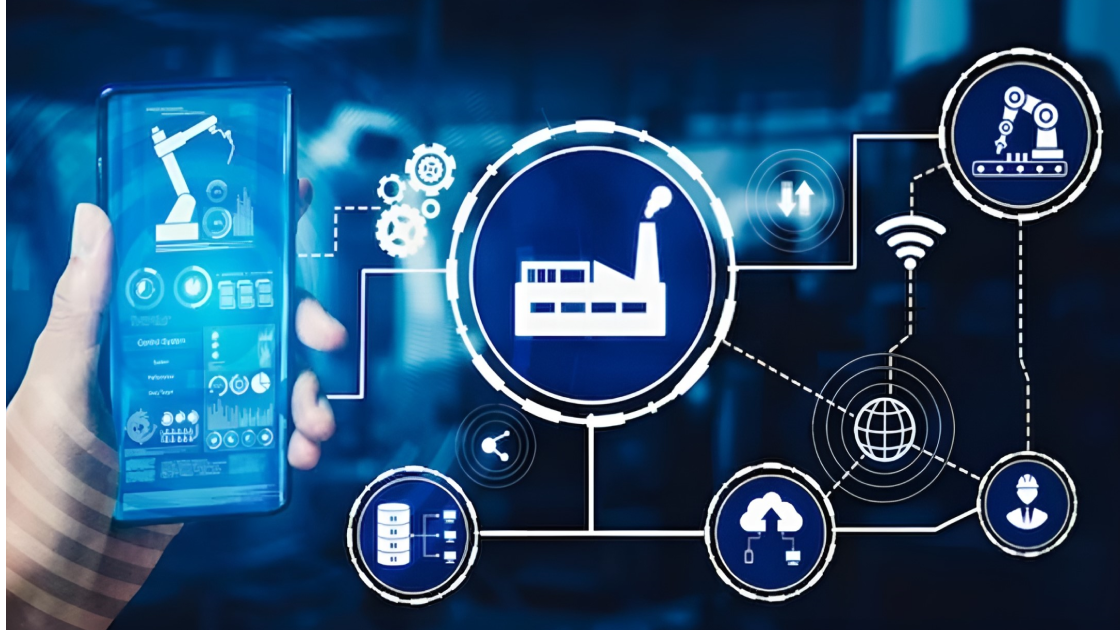
Despite recognizing the considerable potential, many businesses may still not be fully ready to transition to the Smart Factory model. Implementing this solution is often more challenging and faces certain obstacles. Some difficulties for Vietnamese businesses may include: limited awareness of the Industrial Revolution 4.0, insufficient capital for small businesses, limited access to new technology, and a shortage of qualified human resources.
However, do not be overly concerned, as the Smart Factory model is continually researched and improved, even at its smallest components. As technology advances, this solution becomes more detailed, practical, and adaptable to various business types. You can start by transforming the production management of your organization from small, departmental changes that match your needs and capabilities, and gradually expanding as your business grows.
BnK Smart Factory: The Optimal Solution for Manufacturing Businesses
BnK Smart Factory is a comprehensive and advanced digital transformation solution designed to suit various types and scales of businesses. The fusion of Information Technology (IT) and Operational Technology (OT) empowers businesses to tightly manage all their resources. By implementing BnK Smart Factory, the data flow within the factory is interconnected, creating seamless information streams, enabling specialized departments to make timely and accurate management decisions. This facilitates businesses in optimizing and addressing challenges related to Quality, Cost, and Scheduling effectively.
The strength of BnK Smart Factory lies in the intelligent integration and appropriate application of advanced technologies, including, but not limited to:
-- CPS – Cyber Physical Systems
-- AI – Artificial Intelligence, ML – Machine Learning
-- Cloud computing, Big Data
-- Embedded systems
-- Dynamic logistic systems
-- Smart automation technologies: RPA – Robot Processing Automation, DU – Document Understanding, OCR – Optical Character Recognition
-- Wireless communication technology such as Bluetooth or RFID - Radio Frequency Identification
-- Industrial Internet of Things (IIoT)
Within this, IIoT - Industrial Internet of Things, plays a crucial role as the key bridge to create elements within a smart factory.
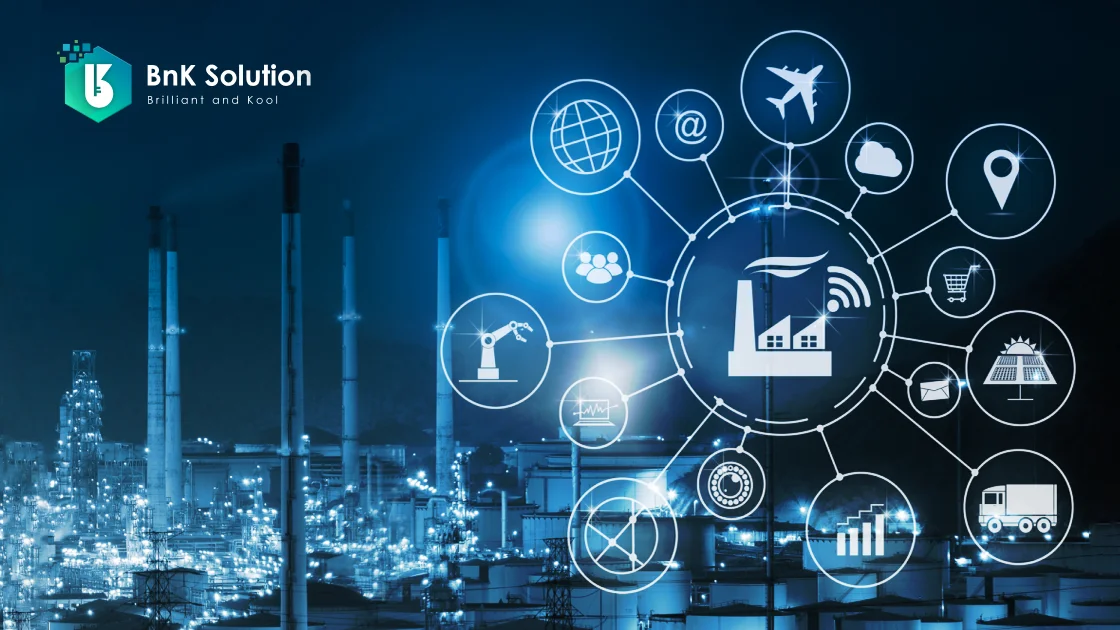
To optimize the efficiency and productivity of a smart factory, businesses need to integrate intelligent systems into the factory, combining them into a cohesive system that operates like clockwork. Information management and production control systems can be integrated, including Manufacturing Execution Systems (MES), Warehouse Management Systems (WMS), Enterprise Resource Planning (ERP), Computerized Maintenance Management Systems (CMMS), and more. This integration aims to optimize the management and production operations of the enterprise.
At this point, you might be a bit perplexed about what your business needs to integrate. Don't worry, when you choose BnK Smart Factory for your digital transformation, our team of experts will conduct an analysis and formulate a strategy based on the specific needs and transformation goals your business is aiming for. We ensure that every step is completed seamlessly from the beginning to the end of a potential project.
Conclusion
The era when workers had to alternate shifts day and night to monitor machinery operation has truly passed. Nowadays, machines and technology can completely replace humans in performing tasks from simple to more complex ones.
Smart Factory is without a doubt, a strategic solution model for manufacturing enterprises in a constantly changing world. Adapting and developing cannot be done in a short time. To maintain a competitive advantage, businesses need to lay a solid foundation for the future. Therefore, start your transformation process now, starting from the smallest parts!
Please refer to our CASE STUDIES for successful stories of customers with the support of BnK Solution or contact our team of experts for advice on Smart Factory solutions!